AHOLD
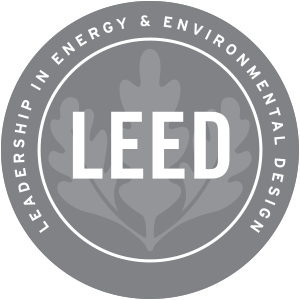 |
LEED New Construction v3 Certified
|
Overview
- Project involved the development of a greenfield regional meat processing and packaging facility for Ahold USA/Vantage Foods. Ahold is the parent company of Stop and Shop and Giant supermarket stores and the new facility provides fresh, case ready, meat products to these store chains through New England, Pennsylvania, and Northern Maryland.
Project Highlights
- Dennis Group provided LEED administrative services for the project which included project credit submission, tracking, start up and commissioning, and final submission to the United States Green Building Council. Upon completion of this effort, the facility received LEED Certified status.
- Specific technical features of the project procured, managed, and constructed by The Dennis Group include a 24,000 lbs ammonia refrigeration system with 5 compressors, approximately 65,000 SF of refrigerated meat processing space, a multi-bay receiving and shipping dock, complete ESFR sprinkler system with a fire pump, and diesel back up generator.
- The facility also boasts a complete onsite waste water treatment facility with two lift stations.
- Site work development included grading, storm water management, parking, and secured access, and a two story employee service area, with locker rooms, cafeteria, and office space.
- The project is currently producing in excess of 1 million pounds of packaged meat weekly. In addition, the project team was able to pass a rigorous USDA inspection of the facility on the first attempt, which speaks to the quality of construction and attention to sanitary detail.
USGBC ® and the related logo are trademarks owned by the U.S. Green Building Council and are used with permission.
CONFIDENTIAL
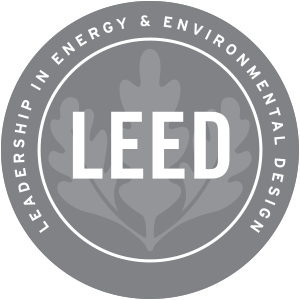 |
LEED New Construction v3 Certified
|
Overview
- In order to ensure long-term competitiveness and meet growing demand, the company decided to build a 300,000 SF facility that embraced the latest equipment and technologies on its corporate campus.
Project Highlights
- This new space, which was located adjacent to an existing finished goods warehouse on their 35-acre corporate campus featured rail receiving, bulk dry and liquid commodities, three high-speed production lines and five portion control lines.
- Dennis Group adopted a phased construction approach in order to seamlessly transition operations from an existing facility.
- Careful planning and permitting were required since the site had several wetland areas. In addition to mitigating the wetland disturbance, sustainability was a key focus of the project since the company has committed to be environmentally conscious and socially responsible.
USGBC ® and the related logo are trademarks owned by the U.S. Green Building Council and are used with permission.
SABRA DIPPING COMPANY
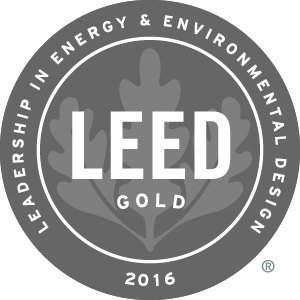
|
LEED New Construction v3 Gold
LEED New Construction v3 Silver
LEED New Construction v2.2 Silver
|
Overview
- To meet rapid growth in the hummus and chilled dips sector, Sabra enlisted Dennis Group to provide full design-build services for the world’s largest hummus facility.
Project Highlights
Named “Food Plant of the Year” by Refrigerated & Frozen Foods magazine
- The initial facility was 120,000 SF which included a 40,000 SF finished goods distribution center – a 100,000 SF expansion was added later in less than 14 months from concept to commissioning.
- Dennis Group took a highly manual operation in Sabra’s former location in Astoria, New York and transformed it into a fully-automated operation giving Sabra a more than 200 percent capacity increase.
- A custom integrated CIP system ensures the product is never exposed to the manufacturing environment and that the finished product is not handled until it has been hermetically sealed.
- The project attained LEED Gold and LEED Silver Certifications for energy savings, environmental impact and sustainability.
- A massive water collection system allows for the reuse of 500,000 gallons of rain and process water each year
- Low VOC levels were specified for all paints, coatings, sealants, adhesives, and carpet systems
- Composite wood products are free of urea-formaldehyde
- Outdoor air ventilation far surpassed the recommended guidelines of ASHRAE
USGBC ® and the related logo are trademarks owned by the U.S. Green Building Council and are used with permission.